I have two tables, one is a SOTA Cosmos Eclipse with a SME V, so a 1 arm 1 table combo. With a suspended deck its really not possible to run two arms on it.
The second table is a Scheu Analog Das Laufwerk No2 which is an 85 pound non-suspended deck with two Dynavector DV505 arms on it. No suspension issues, so it is suitable for two arms.
The phono stage is an Esoteric E-03 that allows for two separate inputs and each side has cartridge loading options. With this arrangement I can compare two cartridges with the same arms (Dynavector) and same phono stage, along with the same drive unit (Scheu)
However my typical arrangement is using an Ortofon MC2000 on one Dynavector arm and the T2000 transformer into a Graham Slee Accession phono stage. The second arm gets a casual listening cartridge like an Ortofon MC3000 I have into one input on the Esoteric. The SOTA has a Transfiguration Audio Proteus on the SME and goes into the other input of the Esoteric.
But with little difficulty, aided by the fact that the Dynavectors have removable headshells I can set things up for cartridge comparisons on an even playing field with little difficulty.
But I did toy with the possibility of one good table. Locally there is a Walker Proscenium available. If I sold most of my analog stuff off I could afford it. But I am not sure where I would put the air pump, and now that Lloyd is passed not sure how to get it serviced if need be, and I think the gold trim on the arm is ugly. Besides I have my doubts how much better it can be versus my SOTA. I am not willing to risk everything to find out the answer to that question.
|
I wouldn’t go near the delicate TT101 (I chose the TT81), however, Halcro, member here did, went thru all to achieve perfection, then proved that the DD motor was able to maintain perfect speed when 1/2/3 arms were simultaneously playing.
I went with the conventional vintage JVC Victor Plinth, he made custom and separate pods for his 3 arms. And, dust cover??? one of the reasons I stayed with the JVC design.
|
It has been difficult to suggest a Densified Wood to be considered for use in the USA as there are not too many Brands able to be found.
Thanks to the TV Series 'Forged in Fire', I have seen a material used that captured my curiosity and have now discovered the correct name for the material that somebody who is developing a curiosity for a Densified Wood might like to look at.
My searching for Diamond Wood, has commonly not found the wood type I was looking for.
A different approach has found Dymond Wood.
This is more like it, a Birch Wood Veneer Board, that begins as a 2 Inch assembly of Layer and is compressed to a 1 Inch finished product with a plastic resin type of adhesive.
The description is very in keeping with the Wood Type I am an advocate of.
The properties that make it more akin is the Weight I have a Dymond Wood at approx' 1300Kg per Cubic Metre, which is undoubtedly a Densified Wood.
The Compressive Strength and stability when submerged in water is very attractive, this material is extremely stable and will not expand or yield in any usage for HiFi.
You could make a plinth large enough to use a M4 Sherman as a Tonearm and it will be the ideal Plinth Material.
Hopefully the info' will be of use to a forum member for their own trials to commence.
|
@pindac Try Panzerholz. You can order from their Canadian distributor BK Industrial. About $1000 for enough to build a plinth. Very difficult to work with, but I managed to complete a 2-arm plinth for my Technics SP-10 MK3.
|
@au_lait I am quite familiar with Panzerholz and Permali, I have some very nice P'mali Boards and am fortunate to have purchased a supply oof P'holz with a friend who has CNC Produced a P'holz Plinth for both of our SP10 Mk II's.
I have listened to the SP10 Mk II in a P'holz Plinth for a few years now, at another friends, and this past weekend on Saturday, was demonstrated one of the CNC Cut Plinths produced for the SP10 MK II, for the first time in my friend's system since it was exchanged from a Marine Plywood Plinth.
The P'holz Plinth has been mounted on to a P'holz Sub Plinth to create a Two Teir Support Structure.
My comments on the last occasion I visited, when a Marine Plywood Plinth was in use; was based around detecting a detractor, of which the fundamental cause was suggested to be from the Cabinet Speakers. I was awarding the Speakers Cabinet as causing coloration.
This Time around, I was very quick to make it known the same Speakers were quite transparent and getting a fix on their placement was now much more difficult, the coloration that was suggested as being present in the speaker's had seemingly disappeared.
A set of Electrostatics were also put to use, and the Cabinets and ESL's were seemingly with parity when it came down to Transparency.
One other point of interest is that on a very well-known Album, I was confident that the replay on this occasion, was delivering information, I had not detected before when replayed on a selection of systems.
The change of Plinth Material in this case has had a notable effect at managing a distortion that can be passed through a Styli, and manifest downstream at the Speaker.
I can't help but think the Sub Plinth has been instrumental in assisting with the additional detail being detected in a replay. As a P'holz Sub Plinth has proved quite a valuable addition to other equipment used at demonstrations prior to Saturday's Visit.
I know the cost of receiving Panzerholz outside of Continental Europe can be quite prohibitive.
Permali is a Densified Wood that is a little easier to find, maybe the licensing for the product is eased.
In general, I encourage a search for Densified Wood as most Countries produce their own Brands, that all share very similar properties, it seems the weight for Overseas Shipping seems to be restrictive, hence the home-produced material.
The Dymond Wood is found in a Board and is found in many colours, this might appeal to a would-be Plinth Builder.
|
@pindac Very nice. Is the sub-plinth beneath the main plinth, or is it a plinth within a plinth? Mine is 6 layers and sits on Townshend pods, but I might build a sub-plinth if I go for a second round.
One thing that decreased my cost importing the Panzerholz was having panels pre-cut and shipped in boxes as opposed to whole sheets that would have required a pallet. I will look into the others you mentioned as well.
|
The Link will help with introducing information, that will supply a broader knowledge of D’fied Woods and show that densifying wood has been an evolving practice for nearly 100 years.
Page 37, shows the Brands that are produced across the Glode, in my humble view, it is these Types of production, when produced to this standard and using the Adhesive Selected, that are the most beneficial to be used for a HiFi Set Up.
Kaiser Speakers use P’holz for their Cabinets and refer to it as Tank Wood, there is a Article on this Company, that has a very good description of the valued properties available from P'holz.
Other Speaker Brands and Kits are also utilising P'holz and Permali as well.
https://www.diva-portal.org/smash/get/diva2:1347640/FULLTEXT01.pdf
|
"With a suspended deck its really not possible to run two arms on it."
Actually it is. Many of us run two arms on
our Michell Gyro and Orbe SE's...
"Very difficult to work with,"
I find Panzerholz very easy to work with.
Sharp tools and lower Rpms. It machines
very well. Its not hard to work with but it is
hard on bits and blades due to the resins
thus the need for lower rpm and less agressive
use of tools to prevent the resins from burning
onto the blades or bits used.
|
It would be great to hear the thoughts of users of Densified Wood or Panzerholz, especially to be informed where they feel the merits of adopting the material has been detected.
I will start by inferring there is strong suggestion being determined that an improvement is produced, resulting from how transferred energies are managed, where a notable difference for the better, is undoubtedly detected.
In all experiences I have had of Panzerholz in use, there is a noticeable reduction of a distortion/coloration being presented through the speaker.
|
I have two tables set up at the moment and a couple more that...well anyway. One of mine is stereo and the other is mono, which if you have room for it and the need is the most convenient option IMHO. Two arms on one TT is awkward for me to use because the arm along the back is difficult for me to reach/use/cue. That is me. I use one phono stage with two inputs and two SUTs. Part of that is just due to practical considerations of space and money. To the issue of need, as a jazz collector, at least in my case, a lot of my records are mono. I mono cartridge definitely outperforms a switch on the preamp and having a mono rig hooked up and ready to go at all times is a life saver as fas as I am concerned.
|
I've been looking at the Acoustand tonearm pods, which would let me add a second arm to one or both my SME Model 10 tables. I have a spare SME M10 arm, and could get an M2-9 for a fourth arm. My phono amp supports up to five inputs. I know, it's crazy, but just imagine having four cartridges on the go at once! Talk about spoiled for choice.
|
The way I'm going to do it is keep my current 1200GR for 78's and a newer, higher-end table for everyday listening.
|
If you enjoy the “art” of turntables and tonearms go for many. I did that at one time and had 4 TT’s and 5 tonearms. I enjoyed the mechanisms of different arms and experiencing the sound differences of different turntables. But later I scaled down to one TT with two arms for my main system. One with a stereo cart and the other with mono. I play a lot of mono Jazz lp’s and love the way it sounds on my mono setup. Have fun
|
It depends a lot on the space available, I have several chains and turntables both with two arms and turntables with one arm, now I am preparing a plinth for the 3-arm victor TT 801.
For phono preamps I prefer phono preamps with multiple inputs.
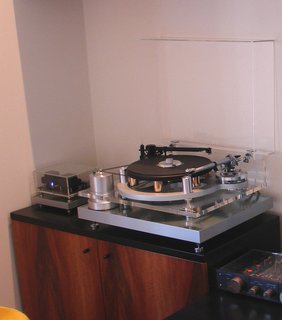
|
e@best-groove The TT 801 is one of the TT's I feel extremely confident would benefit from a Densified Wood Plinth, this material lends itself to Bespoke Design as well.
If not commenced with the purchasing of materials for your project, the D'fied Wood is a material worthy of investigating for its properties for this type of application.
|
@pindac I have original CL-P3D plinth that I would like to use; in the future I will always have time to use diy plinths for the other Victor TT's I own that have remained on standby for the little time I have to dedicate to them.
|
@pindac I use Panzerholz quite a bit. My DIY air bearing turntable uses a platter board made of Pz topped with carbon composite. Dead as a tomb - and quite unnecessary as the air bearing produces no noise whatsoever (it’s air in all 3 dimensions). So that was an unnecessary expense but it looks pretty fine.
The motor board is where a massive slab of Pz really makes a difference. It’s one of several measures to reduce motor noise, and that is down to the noise of the sleeve bearings in a low power precision motor. I've tested that and can demonstrate.
I also use Pz in my DIY air bearing tonearm wand. The cartridge has a very low compliance and couples nicely with a heavy, resonance-resisting wand. What works best is to have the Pz layers perpendicular to the axis of the wand, so that there are hundreds of birch / phenolic boundaries between the stylus and the air bushing.
DIY forever!
|
Dogberry, what phono stage provides 5 pairs of phono inputs?
|
No harm in having a little surplus, when it comes to Vintage TT's.
It's a bit like land, 'they are not making in it anymore'.
Getting the time is crucial to getting the experimentation ventures put in place.
After encouragement to a semi-retired friend over a period of time, they have at present machined a Panzerholz Plinth, and have now used the P'holz to produce a design for a Kaneta Plinth Design, to be used with a surplus owned SP10 MkII.
The end design has been produced and allows for Three Tonearms to be used, of which one can also be a up to 12" inch.
The initial demonstrations/comparisons will be using 9" inch arms, of which one is to be a fixed Head shell Arm, i.e, the SME IV or Audiomods Series Five. There is also an Origin Live 'Illustrious' that might be made available. The fixed Head shell arm will be used in comparison, to the Kaneta Builders own Tonearm Design with a rare method used to produce a detachable Head shell. The third Tonearm Design is the Tonearm both me and the Kaneta Builder own and use, that in this build guise, has a conventional removable Head shell design, and not the most recent Head shell connection produced.
Awaiting their opportunity to be used with the arms, there are two Ortofon Kontrapunk B's in original build guise, that both share similar hours of usage and Two unique types of Bespoke Built Ortofon Kontrapunkt B's, with not too far apart hours of usage.
The original build K'b, has proven itself within the group of individuals I regular spend time with, to be a Cart' that can be extremely impressive through to underwhelming depending on the arm chosen.
One of the rebuilt K'bs to be used, has been used in a variety of demonstrations has been proven to make a very good account of itself.
The earliest talk on the structure of the investigations to be undertaken, will be to learn where the Tonearms are seemingly most noticeable at being effacious in their ability to not impart a sense of mechanical impediment when in use.
For myself, the sense that a Tonearms mechanical function is not having an effect on the replay being presented is a real attractor and a desirable trait.
I personally removed the SME IV and Audiomods out of regular use, for the reason, there was a sense of there being an impediment to the mechanical function being detected. It will be good to revisit this old experience/influence and see, 'what is', in the comparisons taking place.
The method chosen for the demonstration/comparisons will have the beneficial advantage of having little time delay between the demonstration and assessments.
The Tonearm interface with the 'Standard Built K'bs' and the 'Derivative K'b Versions', will certainly be very carefully assessed to see where the attractive and less attractive presentation is to be found.
This will keep a Group of assessors busy for a reasonable period and might also entice other Tonearms to be offered for the assessments to extend.
There has been Talk of Trying out different continuous length wand wires, for a later down the line comparison session when much more is understood.
One Turntable with Three Arms for this type of venture seems quite fitting, Three identical Cart's would be the icing on the Cake, but 'hey ho'.
|
@terry9 A very welcome report, the benefits of use are once more shared.
I once offered a DIY Tonearm Builder a Blank of Permali to be used as a wand material, which was declined. You have seemingly worked out how to use it for this role to its best, with the attention to detail for the laminations.
There are only two other Densified Wood types, I am aware of that would offer more layers of laminations to P'holz B25, one is another Delignit Material and the other is referred to as Picowood. If I read the Spec' correct, I think the compression reduces the thickness of the uncompressed stack by 60%, so more layers are able to be used per given thickness of the end produced board.
|
No question, more is better. My sample of B25 is 19 layers of birch, 18 of phenolic in 19mm, right on spec.
|
2 turntables and a microphone for me.
Beck.
|
"Dogberry, what phono stage provides 5 pairs of phono inputs?"
Five inputs are available in the huge and delightful Musical Fidelity NuVistor Vinyl. It remembers what you have set for each one (each can be MM - with eight capacitative loading settings, or MC - with eight resistance loadings, +6dB or no - which helps to make the output similar such that by changing from one table/tonearm to another you don't have to dash to the pre-amp to alter the volume).
|
best groove
I nearly bought the hard to find JVC Victor CL-P3 Three arm-board plinth.
Luckily, the seller showed a ruler in the photos, and I realized: in order to get a 3rd removable arm board on the left, and not be too wide overall, they moved the main arm board on the right side closer to the TT by cutting the arm board into a curved shape.
Luckily I realized, my 12.5" long arm will not fit. My CL-P2 plinth main armboard is further away, allows my longer spindle to pivot length needed. I’m not sure what the longest arm a CL-P3 fits.
Victor's 7082 long arm is actually only 270 s/p and 12mm overhang: total effective length 282mm (11-1/8")
my blackbird needs 304mm s/p plus 13mm overhang: 317mm effective length (12.5")
|
@pindac Have you tried slate? I have a 50mm Pennsylvania slate plinth under my rebuilt Garrard 401 with excellent results. interestingly, I tried granite and found it to sound quite poor.
|
I have a very nice Slab of 30mm Thick Slate, that I purchased which would produce Two Plinths.
Since my moving away from Massey Plinths, I have not been motivated to use it, or concern myself with learning how it works in comparison to Granite or Corian.
A Granite Plinth has not been experienced for quite some time, and this was with a Garrard 401. The PTP Solid Nine is readily available mounted on Corian.
I only use the PTP now to introduce others to the Idler Drive system and do the odd comparison to show how the TT drives can produce different sonic signatures.
I see the PTP as a very successful method to be used on an Idler Drive system, and in fairness, it is possibly the best use of the amalgamation of a modern design meeting design from an olden era.
I am at present excited about an upcoming experience I will be introduced to.
I see the PTP Design and the Kaneta Design as both coming from a similar line of thought, which is to have the engine decoupled from it usual mounting and attached to a material that is much more suitable for the purpose.
I have been instrumental in presenting this design to individuals who are with the Skill Set in both machining and electronics to produce this design for the SP10 MkII.
The Kaneta Design produced from Densified Wood will be in place for myself to receive a demonstration very soon.
Additionally, it is to be produced to have a New Design Platter.
The Kaneta Design is flexible with Platters, which enables this version to be used with a variety of Platters, i.e, Original, Original Modified, New Design (Acetal with Increased Inertia and a Gunmetal Platter.
The Design is to enable up to Three Tonearms mounted of which one can be a 12" Inch design.
This one has been a long time in the waiting to experience, it is a whole new territory of investigation, and I am chuffed at the thought of it now coming to fruit.
There is also a great opportunity be made available, to compare Tonearms against each other, as within my Group, there are a selection of sought after Branded Tonearms and Bespoke Produce Designed Arms.
Even better is that there are MC Cart's of the same Brand/Models with similar hours that can be donated to get the most from the new experiences to be encountered.
|
I have built several TT plinths - here are my observations
Panzerholz is not stable -it can warp and I would only use it in conjunction with another material that is dimensionally stable.
Granite - rings - no matter how thick.
Slate is ok, doesn't ring like granite due to its stratafied structure.
2 Materials that I have had very good results with are
Engineered Stone ( high quality euro ) 95% quartz. Relatively easy to cut, you can source it cheaply from kitchen bench manufacturers ( offcuts ). Some have CNC facilities which makes it a doddle.
Compressed high density Bamboo ply. It is 50% more dense than Maple, and dimensionally very stable. I use this with my modified Garrard 301 and the result is exceptional. Even my mate with a Kuzma M/4point combo was gobsmacked when he heard my modded Garrard 301 with my compressed bamboo ply/birch ply hybrid plinth - medium mass, rigid, inert.
|
I find that Pz warps only when left unsealed. Is your experience otherwise? Thanks!
|
Modern Densified Woods by their very design are produced to be a material which is low in conductivity and selected for its properties where it is resilient to change when submerged in water, the Spec's show minimum uptake following 24 Hours Submergence.
Drawing on my whole experience of P'holz from the long-time owners, who steered myself toward the material, through to the most recent owners I am in contact with. Where across the Group, thicknesses up to 32mm are in use.
The purchase guidance given has been to buy Cross Grain Construction in B25 with a minimum thickness of 25mm.
There is absolutely nothing made known to me to over many years of knowing P'holz users to suggest a Cross Grain Lamination Structure in B25 of a minimum of 25mm Thickness is showing a tendency to warp.
I have my own supply of P'holz for nearly 18 months now.
A P'holz Plinth Produced, that is not in my possession at present, it is out on loan to an owner of the same model TT, the Plinth is produced for.
Additionally, I have a batch of boards that are cut to a dimension of 400mm x 500mm, I have just put a steel rule across these, and can report there is nothing seen to be considered as a concern.
I am even familiar with a Standard Type Head shell design made from Cross Grain B25 P'holz that is now about six months old. I was handling a couple of the produced Items from a batch only a few weeks past. The Material to receive the Cart' is approx' 4-5mm in thickness, there certainly has not been any obvious signs of showing a deformation.
I have no concerns for the above production specification for a P'holz material.
There is another specification for P'holz, where it can be obtained with a Longitudinal Grain Structure. A board of this at a particular thickness might have a tendency to warp, but I am not familiar with boards created using this Grain Orientation on P'holz.
|
"Panzerholz is not stable -it can warp"
In all the years I have known of B25 Panzerholz ply ,
I have never seen anything even remotely to suggest
it is unstable or will warp. 25 mm and up in my experience is VERY stable to the point of being used
structuraly in many building applications . I have used
pieces removed from the base of massive machinery shipped in the late 70’s that were stored in the factory basement left leaning against a cold damp concrete floor in winter and hot humid in summer for almost 4 decades with zero warps or instability.
The layers of BEECH [its not birch] are layered between with the resins. The vacuum and compression leaves the Beech impermiated with the resins throughout. I simply cannot see any scenario in the home or shop that could cause an inch or more thickness of what is essentionly more phenolic resin than wood now warp or not be stable. Loft condos use it for self supporting stair structures. As far as sealing it, my experience tells me the edges seal themsevles when the blade heats and seals as it cuts. You can literaly polish it to a shine exactly as you would the paint on a car with a polishing compound.
Im with pindac on this claim in my experience for certain. Too many critical items are being made from it whom would not do so without data and reason to hang their shingle on.
Beech B25 Panzerholz, are you talking about the same thing. As my experience mirrors Pindacs and I know of no one elses whos doesn’t...Just know what Ive seen and experienced and never seen proof to refute it...
|
I find that Pz warps only when left unsealed. Is your experience otherwise? Thanks!
Yes. Panzerholz is hard to get in New Zealand.
I purchased from the importer, checked the flatness of the raw material and found the sheets were not dead flat.
Basically I had to laminate 2 pieces, choosing adjacent material and inverting one so that when I laminated the 2 pieces the warp was eliminated. We are talking half a mm across 12 inches, but for me thats too much - I want the arm and bearing to be precisely on the same plain. And I would not want to machine the material flat and disturb the surface - hence the lamination process seemed the best option for me to resolve the warp issue.
Soundwise used as an armboard it damped resonances very well compared to my usual gunmetal armbands. for example it worked well with my FR64S, but these results can be very much dependent on the turntable itself and how the armbands are terminated. For example on my reference TT the armboards are terminated with a 60kg SPZ ( superplastic zinc alloy ) plinth that is as dead as a dodo - on this specific TT the panzerholz armboard is inferior to the gunmetal.
|
Beech B25 Panzerholz, are you talking about the same thing
Never used these words - have no idea what you are referring to.
|
Beech B25 Panzerholz, are you talking about the same thing
"Never used these words - have no idea what you are referring to."
You said Panzerholz and that you used it and it warped.
I assumed then you knew enough about this product that you would know it comes in either B15 or B25. Either 15 layers of Beech veneer per 25 mm thick or 25 layers per 25 mm thick.
I reiterated the word beech as even in this thread others claim its birch wood.
Sorry, I would assume anyone familiar with the product would know exactly what I was refering to...apologies
As far as the panzer armboard being inferior to the gunmetal on a specific table. I can see that preference. Very dead plinth the liveliness that the metal brings would be missed by some so balance is a key here. Its a valid point one must be wary of over deadening in this application where one surface meets another for preference. As far as being out less than half a mm. Its sheet goods not d4s finished stock. For armboards some surface milling like any othe material be it aluminum , brass, stainless, ebony etc. etc...that would be a basic step.
Non of those materials come without the same variations in raw standard plate or bar uniformity.
|
B25 was what I used.
The 40mm compressed bamboo ply I used was dead flat - really impressed with the quality and easy to refinish the surface if required. I used a 60ft bed CNC router used for yacht manufacturing and it knackered the cutter - its a tough material.
Very dead plinth the liveliness that the metal brings would be missed by some so balance is a key here. Its a valid point one must be wary of over deadening in this application where one surface meets another for preference.
or the deadness of Panzerholz could be missed.
My reference TT was specifically designed in the 70’s as an energy dissipation device.
The primary material used, SPZ, was a specially formulated engineering supermaterial, developed in the 1970’s in Japan for earthquake proofing buildings, that has superplasticity at room temperature - any vibration or energy between 10hz to 100hz entering the material disappears through grain sliding at a molecular level. It is no longer available - too expensive to produce.
The secondary material gunmetal is a high lead content naval bronze and was specifically chosen to encourage the transmission of unwanted energy from the arm to the SPZ slab with minimal backward reflection. Having a propagation speed of 2 materials close together improves damping ( sometimes referred to as bi-metallic damping ) and more importantly minimises backward reflection of energy at the material junction - in this case minimises backward reflection into the arm/stylus.
In layman’s terms the greater the disparity between 2 conjoint materials in terms of energy transfer and propagation speeds of any disturbances, the worse the damping and backward reflection is. Something to remember when you are combining different materials in a turntable structure.
Soft material like Panzerholz can absorb a lot of surplus energy, but at some stage that energy has to go somewhere, eventually the unwanted energy will be released in an.uncontrolled manner in terms of time - leading to a smearing of the leading edge in replay.
Ideally you really want a path to ground for the unwanted energy rather than a temporary sink.
|
Firstly, I will make it known, I have a familiarity with the Garrard 401, used in Granite Plinth for a Long-Tem usage. Admittedly this TT has not been owned for approx’ 6 years, time flies.
Recently within my Group two consecutive session were arranged to be demonstrated Idler drives used on the same system. My PTP with a Corian Plinth was the first to make a show, which was mounted on a Sub Plinth using my P’holz Boards. The footer was a AT 616 under the Sub Plinth and the TT. The group had their revisit to an Idler Drive experience, and for the first time experienced one used in comparison to a SP10R.,
The second arrangement was to be given a demonstration of a Garrard 401. This was mounted onto a Compressed Bamboo Plinth, which for me was of interest as I know it is well liked Sub Plinth Material.
The Garrard was given a little better lore than the PTP, as it was mounted onto Two Sub Plinths made from P’holz with AT 616 Feet as the base footer and Sub Plinth Separator. The TT was seated onto Gaia Footers.
The TT had an Origin Live Illustrious with a Sumiko Pearwood Cart’. For the record, I have been introduced to the Tonearm and Cart’ on previous occasions and have been very impressed.
On this occasion in this environment and system, and drawing on recollections, resulting from the very positive impression made, I was to state, this use of the Garrard 401, to be the best performance I have heard from a one, and I have heard numerous over many years during the first decade of the new millennium.
I can’t tell you the Spec for the Bamboo Board used a Plinth, the Spec for the P’holz used is known.
I have investigated compressed Bamboo, and in general the Board is found if ’correctly compressed’ to be a weight of approx’ 700Kg per m3.
A newer to the Market Dense Bamboo - ’Tiger Bamboo’ is to be found at a weight of approx’ 1000Kg per m3.
None of these are plasticised through using Resins as a Densified Wood is.
In general Densified Woods are found at approx’ 1200Kg - 1500Kg per m3, of which P’holz falls in at around 1400Kg.
I have been a follower of the individual who may have put the information forward, that identified Densified Wood as an attractive material for Plinth Building Purposes. The Web Pages containing many useful comparisons to other materials and the criteria used for measuring a materials damping factor is to be seen at qualia.web.com
I have in the past discovered alternative materials of interest and sent in material samples to be tested by the producer of this Web Site.
From my understanding it is Densified Wood that is the most efficient at managing Transferred Energies, in a manner that will reduce the level of superfluous mechanical energies migrating to the point it reaches the Styli and impacts on the Signal Path.
|
I find it interesting that beech is used for making a resin impregnated wood. Beech has a reputation as being one of the most waterproof woods available - it used to be used for the construction of waterwheels at mills and is still used as handles for shaving brushes for that reason. No doubt the pressures used in the impregnation manage to overcome this resistance, but all the same, there are woods that would be far easier to impregnate.
|
Panzerholz is not a "soft" material.
Beech is chosen not for being waterproof ,
but because it is one of the hardest woods
and with high rigidity. Whether or not panzerholz
is your preference to use through experience
or not is all fine but the lack of basic knowledge of
it from its ingrediants to why they are chosen seems to undermine the relevence of "opinions". Long wordy explanations of what is basicly constrained layering
wont change the way some hear and choose. The popularity of light weight Rega tables proves that.
I’m quite certain that a slab of panzerholz can dissipate
the energy of a turntables self noise and the music
playback in its environment . The foundation it sits
on is actually a seperate problem.
Solve that first , ....
Besides we're off track on the OPs
original question...
|
"I'm curious to hear how people would decide for themselves the answer to this question. Or maybe you've already made this decision - what do you like about your decision or what would you differently next time? "
Cheers.
" Besides we're off track on the OPs
original question... "
There are those who not only like to have an option on how many Tonearms are mounted to work with one Turntable, but this can also be achieved through a design that is not offered by a TT's Manufacturer. It is achieved through an individual deciding on a Material to support the Turntable and Tonearm/Tonearms.
Hence P'holz has come into the discussion, as there has been earlier discussion on Bespoke Plinths being produced, to support the usage of Multiple Arms.
|
It is compared to boronized steel!
Panzerholz is not a "soft" material.
|
One turntable with two arms, or two turntables with one each - which would you prefer?"
I said "original" question...thats it above.
Evolved or not the thread topic is multiple arms
or not for personal preference.
Now with the brilliant deduction that borinized
steel is harder than wood I suppose your back
on track...
|
I have 3 turntables mounted in slate plinths, using Pennsylvania black slate. (I assume not all slate from all sources is created equal.) The quarry in PA that sold me the slabs also was able to hone both sides of each slab perfectly flat and champfer the edges. Then in York, PA, I found a waterjet company that "learned" to cut my 3 slate slabs so to fit respectively, my Denon DP80 (50mm thick), my Lenco with PTP top plate (50mm thick), and my SP10 Mk3 (75mm thick). In the case of the Mk3, the slate alone weighs about 75lbs, after cutting out the hole for the chassis. I had a subplinth made out of solid cherrywood, for the Mk3 only, and bolted that to the bottom side of the slate slab. I tell myself I can hear a tick better performance due to combining slate with cherrywood. This all sounds very good to me, but once having made the effort, I would not do it again. Nor do I fret about whether or not Panzerholz or some other material might sound better. Suffice to say I think all these materials are excellent choices. Slate is just the road I went down. I also agree, granite not a good choice; I don't really know what it is about the internal structure of granite that makes it less suitable than these other materials.
|
maybe @dullgrin would like to make a further follow up contribution to confirm if the information offered since his last contribution, is satisfactory to help with the initial inquiry made.
" Nor do I fret about whether or not Panzerholz or some other material might sound better. "
The journey for myself through HiFi Encounters and building a HiFi System, is based on growing in experiences through being demonstrated different options that can be incorporated into an owned system.
I don't see myself as a lone entity in this understanding of a Journey with HiFi as the interest.
There is for me, a pursuit of knowledge, especially about how one is stimulated by the use of certain components or an assembly of certain components.
As one's experiences grow, they are quick to identify where a stimulus is present that is an attractor or a repellent.
As one's experiences grow, the likelihood is that there is a much more selective mind set in place, and a willingness to change prevails, the stimulus encountered can prove to be very persuasive. To the point an outright rejection of an idea or immersion into an idea takes precedent.
I am not one who is to Stagnate and be found Resting on One's Laurels, and especially not one who will Show Contempt Prior to Investigation.
There are tremendous discoveries to be made, when a mind is open to what others are doing, where differences are obvious to one's own choices.
It is with the open approach and willingness to learn that new discoveries have been very persuasive, bringing change, hence I was introduced to Plinths produced that were very different to my 'one time favoured' Mass Material Plinth Design. With the result being the Mass Material Design are no longer favoured and wanted to be used as the regular method.
|
@lewm With respect to granite, presumably the crystalline nature of rocks can affect their ability to resonate? All I know about them is to do with their abrasive qualities when lapped and used for honing straight razors. And now I shall be accused of going off topic again, so...
My plans for tonearm pods are underway. They will be made of brass rather than stainless steel, and black ceramic coated just for visual matching purposes. SME mounting plates on top, and three spikes underneath. The mounting plate will be precisely 90mm above the tips of the spikes, which is the same as the built in arm plates on the Model 10 tables. My next choice will not please everyone: I shall place a pair of SME M2-9 tonearms on them. These are pretty much like the 3009, but straight instead of curved, using 309 type headshells instead of the 3009 type, and have a damping trough. I have half a dozen 309-style headshells being one reason, and trust in the wisdom of Alastair Robertson-Aikman is another. It will probably be a couple of months for the machinist to finish the pods, so I'll have to be patient in the interim.
|
Thanks for the interesting conversation, everyone. I've been reading with interest all the responses.
This thread, for me, was not so much a 'tell me what to do' or 'help me make a decision' type thread, more conversation starter, born of a genuine interest in how others approach their desired analog playback chain. I don't think there's any universal 'right' answer - just what works for each of us. It's interesting to see the responses.
I will say that my interest in the topic arose as I started to think about a second, all analog system. I've had a turntable in my system for at least 20 years, now, about as long as I've been in the audio hobby.
Over the last couple of weeks, I've assembled that second system - with the assistance of some great dealers and distributors. They're out there. Shout out to the teams at Kevalin Audio, Next Level HiFi, Bluebird and Nashville HiFi (no affiliation, just a happy customer - they all have been fantastic to work with and I think they're worth knowing about).
For now I've landed on one turntable and tonearm in my main system, and one in my second system. Neither of my current tables really has an option for a second tonearm, so I will look to add another table - maybe with two tonearms, maybe not - to the second system once my checkbook has recovered (!!!!). Adding a dedicated option for a mono cartridge in the second system is my next goal.
In any case, thanks for the responses all. Keep 'em coming. And happy spinning.
|
@dullgrin Thank You for a very fair assessment and your encouragement.
|
@dogberry Both Natural and Manufactured Stone has been regularly seen in use as a Plinth Material for too many years, the Trend I recollect commenced in the 90's with the Garrard 401 being championed in a Company called Slate Audio's Slate Plinth. The Trend grew to other Decks and even Speaker Cabinets.
Not all can successfully Market Slate, hence new Natural Stone was becoming more mainstream, I chose Granite as my material, as I preferred the demonstrations of Granite on a 401, to those I had been to when Slate was demonstrated.
Being brutally honest, I may have even been more attracted to Granite as I preferred the individuals that were advocates of it for the purpose as a Plinth.
Within my HiFi Group, one member has a paraphernalia of ideas, why Slate is inferior to Granite as a Material to be used within HiFi.
I am not without Granite, I utilise it in plenty of places within my System, but mainly now as one of the materials used in an assembly of various Materials that functions as a Structure.
I am also an owner of Manufactured Stone as a Plinth, which has the Brand Name Corian. Again, this is another material I have chosen not to use as a regular choice, it is pretty much reserved for demonstration purposes.
My Friend who has recently converted to Densified Wood - Panzerholz, has a quantity of Corian in Slabs, as the P'holz has been capable of persuading them to rethink their previous thoughts on Plinth Materials, they are remaining curious, and are in the process of utilising the Corian, to try this material out as a comparison.
Lucky for me I will be able to hear this in use, on a TT and Tonearm of the same design I own. This will allow for Two Set Ups to be used of the same equipment mounted on two different Plinth Materials, additionally this will also allow me to have my Cart' used during a demonstration along with the Two standard Ortofon K'bs available.
If all seems worthwhile, I do believe the Kaneta Designs will be produced in both materials, to take the investigations further.
@dogberry In relation to your notification of your next venture to have a Standalone Tonearm Pod Produced, to be used with the SME 10 and SME M2-9 Tonearms.
I have no doubt the Headshell Design used on the M2-9 is a much-improved mechanical interface over any Products it Superseded from SME.
It does not matter one iota, who is pleased, you are the end listener, and you are the one making choices for how monies are used that leave your account.
I am sure you are to share in many hours of fun filled investigation when these arrive at your home. I sincerely hope there will certainly be a room full of music on a regular occasion.
If it is off interest, the answer does not have to be immediate. I can donate to you, to assist with having an extension of the experience of a Tonearm Pod, a piece of Densified Wood - Permali that is a 75mm (3 inch ) Thick Material, cut to a dimension that would suit having a Standalone Tonearm Pod produced from it.
Let me know, there is no rush.
|
Very kind of you, John, but I shall decline. My two turntables sit atop a very heavy 17th century oak chest, which I have carefully levelled. I don't think a slab of anything, however good it is in the audio realm, will be acceptable to SWMBO.
I started out just trying to find a cartridge I could live with when my London Reference is finally done, and I ended up with a handful of rather nice carts and a second turntable! And now the madness proceeds towards four tonearms...
|
@dogberry It is not madness to have a plan in mind for Four Tonearms, it is a little unusual to have four in use consecutively, but definitely not unusual to own Four Tonearms and a selection of usable Cart's to match that number or more even.
I have owned and used approx' Nine Tonearms to get to the place I am today with a Tonearm.
Today with only one Tonearm in use, I still have a selection of Seven retained, along with LOMC, HOMC and MM Cart's, all with a usable number of hours left on a Stylus. I don't know how ageism may be affecting some through the time in storage.
As for the offer for the Permali, the offer is for a piece of the size that would be able to be turned into a Tonearm Pod, that by design, when finished will be able to be stored in a cupboard when not in use, or only be as intrusive as a Black Brass, if kept in use.
A Slab to not be accepted by SWMBO will be very expensive to send onto you.
I was given my own room without any dispute for the HiFi, it was like an approval to go off the scale with madness. To get the idea, the Power Amps are seated on a 250Kg slab of Granite. In the Room I would refer to that one as adventurous.
There are more quirks to be found.
|
I am also an owner of Manufactured Stone as a Plinth, which has the Brand Name Corian.
Corian is about 1/3 resin 2/3 mineral.
Engineered quartz stone is 95% quartz / 5% resin.
These materials are quite different. I would never describe corian as a manufactured stone.
|
Corian is potentially the earliest form of a Composite Stone to be produced an available mainstream material, it has a Patent, and it is this Patent that is the fundamental guidance referenced to produce alternative Composite Stone products that followed.
It is hard to see how a 66% inclusion of Bauxite Stone with the rest as an Adhesive Resin, used in the mixture for Corian, disqualifies it from being termed as a Manufactured/Engineered Stone.
|