And your method for arriving at a numerical damping factor with plinth materials, Pindac?
We also have to ask where is all this spurious energy coming from? Also keep in mind that European slate is different from Pennsylvania slate, just as PA slate is different from Vermont slate, etc. ( I’ve had SP10 mk2 plinths made of both. PA slate was better.) OMA proudly use PA slate and also natural hard woods from PA in their speakers.
Slate is layered such that its energy dissipation in the plane parallel to the layers would be very different from its energy absorption perpendicular to that plane. There you would probably get more “bounce back “. But does it matter? What spurious energy is attacking the surface perpendicular to the plane of the layers? In the end also, slate provides lots of dead mass, which I think is beneficial. Finally it’s impossible to resolve the question by back and forth discussion. I built my plinths 10-15 years ago, I’m satisfied, and I’m not starting over with plinths.
Typing on my bespoke cell phone made of densified wood.
|
@lalitk
+1 for Woodsong renovation work (I have a TD124).
VG results (for TD124) with "Governor" PSU made by Deco Audio in UK for rational cost: lower noise floor, greater impact.
I have VG results after milling -- using pillar drill-- a solid plinth of German "Permali" wood: twice density of baltic birch (similar if not same manufacturing principle of "Panzerholz"). Plinth stands on decoupling tripods. Image of this posted on my system page. Material of modest cost - around 100GBP.
This set up sounds fast, detailed and richly musical. As others noted, slate may be less optimal. I have found wood somewhere in plinth or under, as support, gives more natural sound with less edge. YMMV.
|
Just as Damper and Body Materials used in Cartridges has evolved in the selection for a materials.
Materials used for structure in audio equipment has evolved as well, and it is easy to see where the industry is adopting it and not. Linn won't inform on their most recent TT being constructed with P'holz, it is an inhouse name for the material. As does Kaiser Speakers referring to the Bespoke Materials as Tank Wood.
There are most likely other Brands with a usage of it and a disguised name to protect their IP.
'Bounce Back' is a simplistic term, used when describing extremely Poor Dissipation and Damping, the Energies are not Damped or Dissipated, hence they are contained and in motion as further transferal, hence 'Bounce Back'.
In relation to the TT, being in contact with such a material, the likelihood/guarantee is that the Styli is to be receive energies from Bounce Back, resulting in a contaminated energy being sent to create the initial signal to be transferred for further stages of amplification, where the contamination is included in all stages until sound is produced.
Whether the end listener is able to detect the contamination in the produced sound will be open to debate, I have and do, when certain types of structure are being used.
|
@mdalton, @fsonicsmith, @noromance
Thank you for the great insight on your journey and for sharing your collective experiences with Garrard 301 / 401. This is exactly the kind of feedback I was hoping to read! I did initiate the purchase of a Garrard 301 with full restoration, finished in Sable (black). The ETA is 4-6 weeks.
As far plinth goes, I had the same vendor in mind on eBay as @elliottbnewcombjr linked above. Based on what I’ve learned here, I am going to query the plinth maker about the manufacturing process, materials and footers. I plan to experiment with the footers and eventually decouple TT with a SRA Isolation base atop my excellent core audio design rack.
As far cart options, I am taking notes on all the recommendations so far. Three extra head shells are already in-house with Reed 3P tonearm :-)
Hopefully, Garrard 301 ends being my end game TT!
|
I use slate combined with cherrywood in two layers, for my Technics SP10 mk3. I listened to it befor and after adding the cherrywood base. It seemed a touch better after cherrywood was added.
Pindac, hoe did you assign a numerical value to damping factor for a plinth? And can you define “bounce back”? Thanks.
|
@pindac @noromance @fsonicsmith
all interesting. My only experience is of Woodsong plinths. Didn’t realize, but apparently they combine birch ply, panzerholz, and slate, all in one design. (search for an Art Dudley piece from June 2016 describing a Woodsong 301 plinth.) Does that mean I win? (lol! quite sure we’d all love each other’s decks!)
|
I don't use Slate for any purpose in HiFi, but have at one time been interested in the material and as a result, own a very heavy Slab, probably from a Seam that was close to 2500Kg+ per m3.
I no longer express an interest in Granite as a Plinth Material, I have many years experience of it used on a 401, and through the 401's new owner being a friend, experienced the 401, used on a selection of Plinth designs of which I preferred the lighter designs, in either a Wood Mass with Damping Pockets or as a CLD Design.
I know the 401 Sound very well and the most it has impressed me is during one of my last encounters of it in use, when the 401 was mounted in a Three Way Compressed Bamboo Board cut to be used as a Plinth.
I stand by my statement made at the time of the demonstration, being that I have not encountered a 401 that could create such a good impression.
With my better understanding of materials today, I do know that the Three Wat Compressed Bamboo Board can have a Damping Factor of 2 - 5 depending on whether the size tested is a Sample dimension or a Plinth Dimension.
That as a measurement for a Sample is 10x improved damping in comparison toa MDF Sample.
Slate as a Sample has a measurement of 0.017, which is one the last measurements one would select if choosing a material with highly effective intrinsic damping. The Bounce Back of Energy transferred is going to be evident, I will state audible, if compared to a material being used with damping properties that produce little or negligible bounce back of received energy.
The material I am now an advocate of, and for a period of time have been transitioning to for various roles. Especially as a Plinth Material, Sub Plinth Material, Equipment Chassis and is the material that will most likely supersede most support materials used in my system is the material referred to as a Phenolic Resin Impregnated Densified Wood, of which it can be discovered from the Brand Panzerholz and Permali and in my case are both owned.
A Sample of Panzerholz and Permali has a Damping Factor of 4 and a Plinth Dimension of 25mm Thick Panzerholz has been measured with a Damping Factor of 7.
There is no Bounce Back that is audible from these Damping Factors, and the Dissipation of Energy transferred is one of the Best Measured as well.
I will not suggest a Stone, Plywood Board or MDF is a inferior plinth, each material can be quite stable. I am sure they have their fanboys for how the sound produced is assessed.
I would myself have a Compressed Bamboo over any of the above, as I know how it has impressed me in relation to what I know about Stone and Plywood Board Designs.
Over all the above I now know without reservation I would have a Phenolic Resin Impregnated Wood Board, I have heard this compared to Marine Plywood, MU25 Plywood and the Panzerholz Plinth was instantly discernable for the improvement it offered.
|
Fsonic, My own Lenco is mounted in a 50mm slab of PA slate. However, it also benefits from a PTP top plate, a hefty after market bearing, a platter that has been painted with vibration reducing black paint, speed that is regulated by the Phoenix Engineering gear, and two high end tonearms. So I am hardly in a position to say that the slate slab alone is responsible for its excellent performance. But it doesn't seem to hurt, either. I can say I replaced a John Nantais re-plinthed Lenco with the one I have now. the JN unit did not benefit from the PE power supply and Roadrunner, and the slate unit is better for whatever reason.
|
@fsonicsmith
I know we’ve posted on this before in previous threads. The more things change, the more they stay the same, huh? I’ll reiterate for this thread. As far as comparing the two plinth technologies, I have a 5 x 13 layer solid Baltic birch ply 12" arm plinth topped with 1/3 solid walnut and "veneered" with 1/2" maple. I also have a 50mm PA slate plinth. 2 Audiograil 401s. Modified with 3rd party idlers, bearings and platters. 2 Jelco TK 850L arms. Same Decca London cartridges. They both sound great. I’ve compared them side by side. The slate one is more transparent, airy and neutral, gets less confused, blacker backgrounds, faster etc. I would temper this with the clause that if one likes a warmer, tubier sound, the slate may be the proverbial cup of tea. As far as damping, soft PA slate (amongst other) is made up of layers which defract and absorb noise.
Slate is not known for absorbing or damping motor vibration or any other vibration.
|
I have 3 TT s in PA slate and am very pleased with performance but I did not sample a wide variety of materials so would not claim slate is absolutely the best. So what do you prefer, fsonic?
Hi Lewm. I would love to claim that I have tried a slate plinth with either my TD124 or 301 but that would not be true. So when I responded above that it is not true that slate is optimum, I did so brashly and from trusted wisdom. That said, I went through a series of turntables starting in the early 2000's and then started focusing on idlers in the last fifteen. I have talked at length with many experts. I have experimented with several different wood plinths and with multiple platters on both of my idlers. Unfortunately our niche (idler drive turntables) within a niche hobby does not result in very much scientific analysis of matters such as vibration damping properties of alternating layers of birch vs. slate. If you do some research you will find some good threads on the Lenco Heaven site. Slate is not known for absorbing or damping motor vibration or any other vibration. Our lizard brains just assume that slate being heavy and massive it must be good for something like a plinth.
I have no doubt that a Garrard 301/401 can sound very good mounted on a slate plinth. My unsupported belief is that the sound you will get is not consistent with the best characteristics of idlers. To draw an analogy, why would anyone take a Harbeth loudspeaker and convert the enclosure from wood to Magico-style alloy keeping everything else equal?
|
|
I have 3 TT s in PA slate and am very pleased with performance but I did not sample a wide variety of materials so would not claim slate is absolutely the best. So what do you prefer, fsonic?
|
Soft Pennsylvania slate is wonderful. Silent and brings out the speed and detail. I've three 401s in different plinths with 50mm slate being the most capable.
Slate is not optimum. Sorry but just true.
|
Slate is not optimum. Sorry but just true.
Agree that having a concrete slab floor is preferable to being over a basement with floor joists. But most of us don't get to design our houses and listening rooms (though in my case I did) and many of us like having a full basement.
Btw, if you get a speed control unit such as the LDA, remove the eddy brake.

|
Consider using a slate plinth. More detail, speed, and air. Pay attention to the surface you put the turntable on. Wooden tables don’t sound great. Concrete floors are preferable.
|
I would forget history, get it to be my main TT.
get the great TT, get a great tonearm with removable headshell and a modern MC cartridge of choice, optional cartridges on headshells waiting for their turn. It could compete with nearly anything.
My Thorens TD124: I used an SME-3009 II Tonearm with Shure’s last great MM: V15Vxmr, beryllium cantilever, micro-ridge, tracked at 1.0 g. I think a part of the ’best bass’
Tonearm: consider ease of adjusting arm height, not so much for perfect VTA, more for if planning on a few cartridge bodies that might be slightly taller or shorter .
Others exist: I have installed:
my Acos Lustre GST-801, loosen by hand short arm locking lever, turn for up/dn, tighten (easy, smooth, adjust while playing)

my Russian 12.5" arm, has micrometer for fine height adjustment, BUT you have to loosen two allen set screws (after you find the right size allen key), so: precise but not a quick change for a different cartridge. (not removable headshell anyway, I just mean: micrometer, precision, if not easy ...)
Two Micro-Seiki 505’s for a friend (just mounted two new cartridges for him this past Saturday. Loosen short locking lever by hand, move up/dn, lock by hand, easy, however not as smooth as Acos, I would not do it while playing. Quick enough, simply lift arm up, adjust by hand, arm back down.
Another feature these arms have is an adjustable fitting for the headshell to set azimuth. loosen tiny screw, rotate fitting a speck, tighten tiny screw.


Technics EPA B-500 tonearm base, wonderful: unlock by hand, turn outer ring by hand, lock by hand. Same as Micro-Seiki, not while playing: unlock by hand/lift/adjust/down, lock by hand
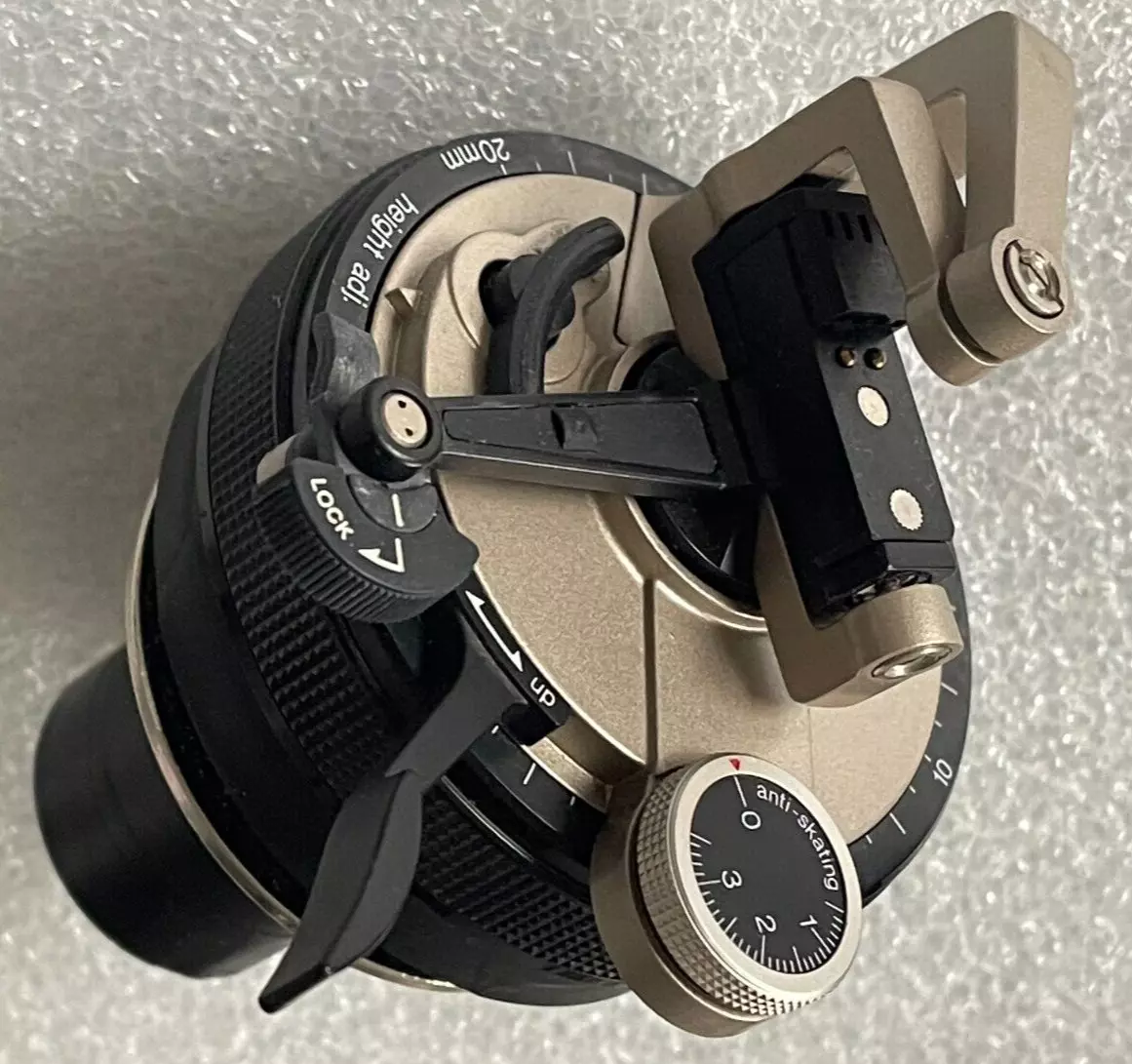
the up/dn lever is to raise/lower arm, the lower outer ring is arm height.
this base allows switching arm wands also, another way to have different cartridges ready to go. the S arm wand is removable headshell; straight arm wand is fixed.
|
|
Never heard a Garrard 301.
I loved my similar era Thorens TD124, it’s 11.5lb platter the reason for (your words) ’drive and impact’, best Bass I ever had. If my wood floors were not so springy I would still be using it.
I see some very tempting Garrard 301 restorations with custom plinths.
Personally, I would get a plinth allowing two tonearms (add 2nd arm in future?)
and a Dust Cover, thus consider the shape of the Plinth, and it’s appearance with dust cover on. You can get new dust covers easily, any size, a rectangle easier and less costly.
Many beautiful Plinths exist, but do not plan for dust covers, i.e. this maker uses many exotic woods

|
A Garrard deserves a London Decca Reference cartridge both for historical reasons and to maximise the liveliness. Should be available again by the end of this year.
|
Thanks for the mention lalitk.
As the photos in my profile show, I favor a large plinth, as large in all three dimensions as your rack can accommodate. Forgetting about any thought process that a massive plinth absorbs vibration, the real estate on the top allows for all arm lengths without a cantilevered arm mount hanging off of the edge of the plinth.
Unfortunately it appears that Russ Collinson has moved on from plinth building. The alternatives for a quality plinth are pricey. Stay away from the two different plinth builders seemingly based in Muldovia seen on eBay. I have one sitting idle in by basement where it will likely remain.
The Reed arms are a bit tricky to mount because the mounting template supplied by Reed is confusing to use. You are going to need a bit of patience or the assistance of a Reed dealer to mount its P-S in such a way as that your cartridge can be optimally aligned.
Your choice of rack for the deck will be critical. I use Symposium's rigid (non floating top) model. The rack should be massive, offer good isolation from vibration at the top shelf, and should offer leveling footers.
The IEC and PC imho are not important. I have had no compatibility problems among a broad range of cartridges, currently a Lyra Etna SL and a VdH Crimson Strad XGW.
I use Stillpointe footers under the plinth. Though more willing to be of assistance if you are buying something from him, Steve Dobbs (Xactaudio) is a great source of information.
As I think I told you in a PM, I chose to go with an aftermarket heavy duty brass bearing from Ray of ClassicHifi in the UK. And that is despite the fact that my 301 came with a NOS grease bearing (which I have kept for later use one day).
|
I’m obviously a big fan of idler drives, as I have a Thorens TD-124 in addition to my 401. I’ll give you a brief synopsis of my journey with the 401:
- Purchased it on ebay from a UK seller; had it shipped directly to Woodsong Audio (Chris Harban) in Idaho. It was not in as good a shape as described on ebay, so Chris did one of his full restorations. All the steps involved are listed on his website under “Garrard 301 Restoration”.
- I decided to have Chris repaint the chassis in piano black; this was because the stock gunmetal color would not have looked very good with the blue I had picked for the plinth. Why blue? To match the Italian tube integrated and phono pre I was pairing it with. Some traditionalists may have a problem with that, but it turned out stunning, and is now one of the turntables featured on the Woodsong website. (pretty cool!)
- Chris installed an IEC outlet on my 401, but I don’t know what brand. A couple years ago I replaced a stock pc with a straightwire gray lightning. Nothing particularly expensive, and I can’t tell you it made a difference, but my own experience is that PCs are more important on the amp and phono pre than on the TT. Also keep in mind that I’m using the original motor, so ground is floated on the IEC outlet anyway.
- Regarding the stock motor: I’ve had the 401 for 6 years now, without any servicing. Since my deck was a UK version, the strobe light wouldn’t have worked correctly on the platter markings, which assume a 50 hz signal. So Chris didn’t bother to get that working. Well a month or so ago I installed an LED strobe light conversion kit on the turntable and guess what? Speed is still spot on 6 years later. The speed adjustment dial is still set at noon. Pretty remarkable. Great engineering by Garrard and great restoration by Woodsong. So I’m not sure I’d recommend an external speed controller.
- Regarding the tonearm and cartridge: I went with the 12” Reed 3P (Cocobolo); got an amazing deal cuz Chris had a demo he needed to move. I originally paired it with a cheap Hana EH knowing I’d upgrade eventually. Landed on Koetsu Urushi Tsugaru, well, for three reasons: (1) It’s gorgeous; (2) Koetsu was always a destination cartridge for me because, well it’s a Koetsu! (3) Sugano San originally voiced his cartridges on a modified 401, so it was meant to be.
That’s pretty much my story. I have one last step in the journey. Am about to upgrade my step up transformer to something more befitting a Koetsu. Am very satisfied with the setup.
Hope that helps, and am happy to answer any questions you might have.
|
I have heard the 401 with the LDA Speed Controller Prototype and the Marketed Model.
I have also heard the 401 using the LDA Speed Controller compared to other Speed Controllers, produced as designs to be DIY produced.
I do believe the LDA is the better as a basic design to a DIY basic design, but have heard a bespoke modified DIY Basic design that was parity or possibly a little better that the LDA on both a 401 and a GL 75.
I use a Nigel Built (Personal Built Model) NSC on my PTP Solid 9.
I know the Idler Drive Sound very well and have encountered many ID's including the 301's, I have heard these models in a large selection of Plinth Designs, but not all demo's are in the home system.
A good selection are in systems I know quite well.
I today find the DD TT, especially in my own case, a Vintage Japanese DD TT, when mounted on a particular plinth type, is much more attractive to my unique preference as a method to replay a Vinyl Album.
|
Jim @jperry
Thank you for your recommendation on PS. I am familiar with your fine system and may have conversed with you in the past. How about this for coincidence, I used to own SME 15AV with Hana Umami Red cart 😊
|
@lalitk,
I had a SME 10 and went to a Garrard 301. Never thought about looking back.
I'm not sure if a power cord makes much difference, but a power supply like Long Dog or Hanze does make a difference.
https://www.longdogaudio.com/product-category/power-supplies/
My system is posted if you want to look.
Good luck with your Garrard journey
Jim Perry
|