an insulting price,
Denon DK-300, $354. in 1981, including the dust cover, 65mm thick

JVC 7 layer composite plinths are 59mm thick, also with dust cover
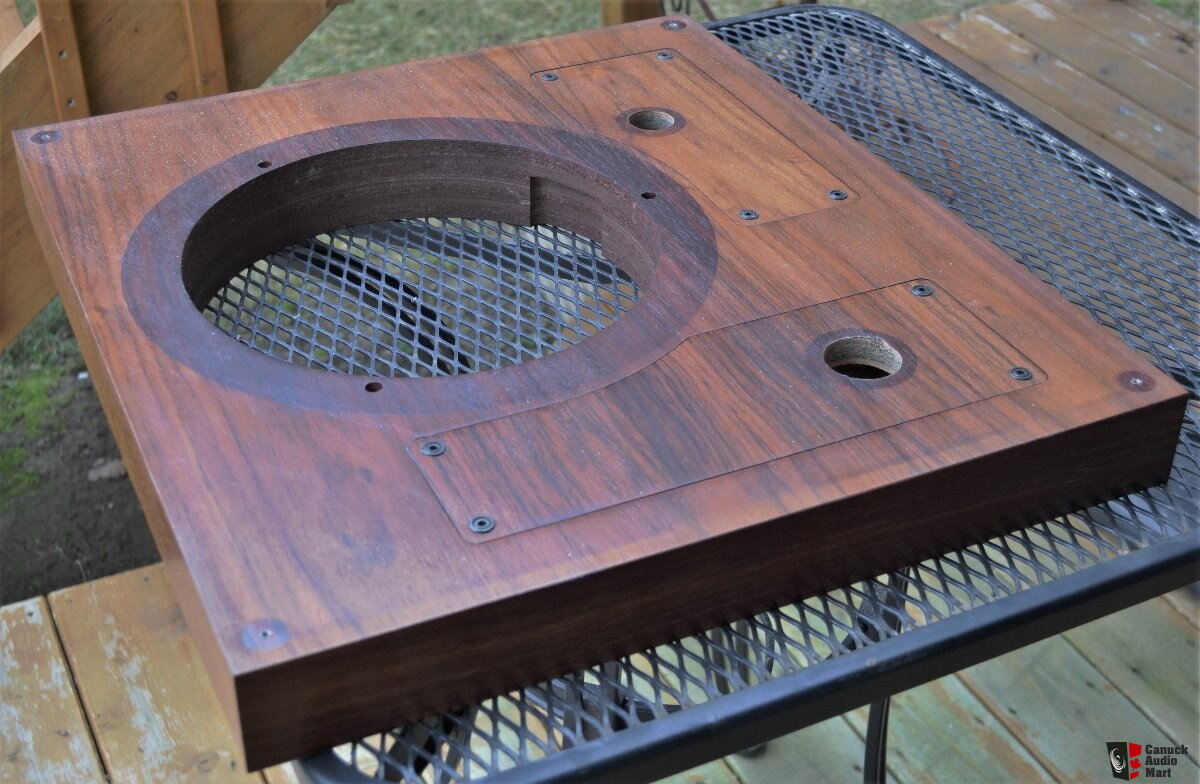
Linn's is 66mm thick, no special composite, just beechwood, glue, pressure.
Sony made a rare composite plinth, I can't find it quickly, going out the door now

|
It’s Insulting to every person alive and not yet born.
And no research, no new technology, I prefer the look/scale/properties of Baltic Plywood
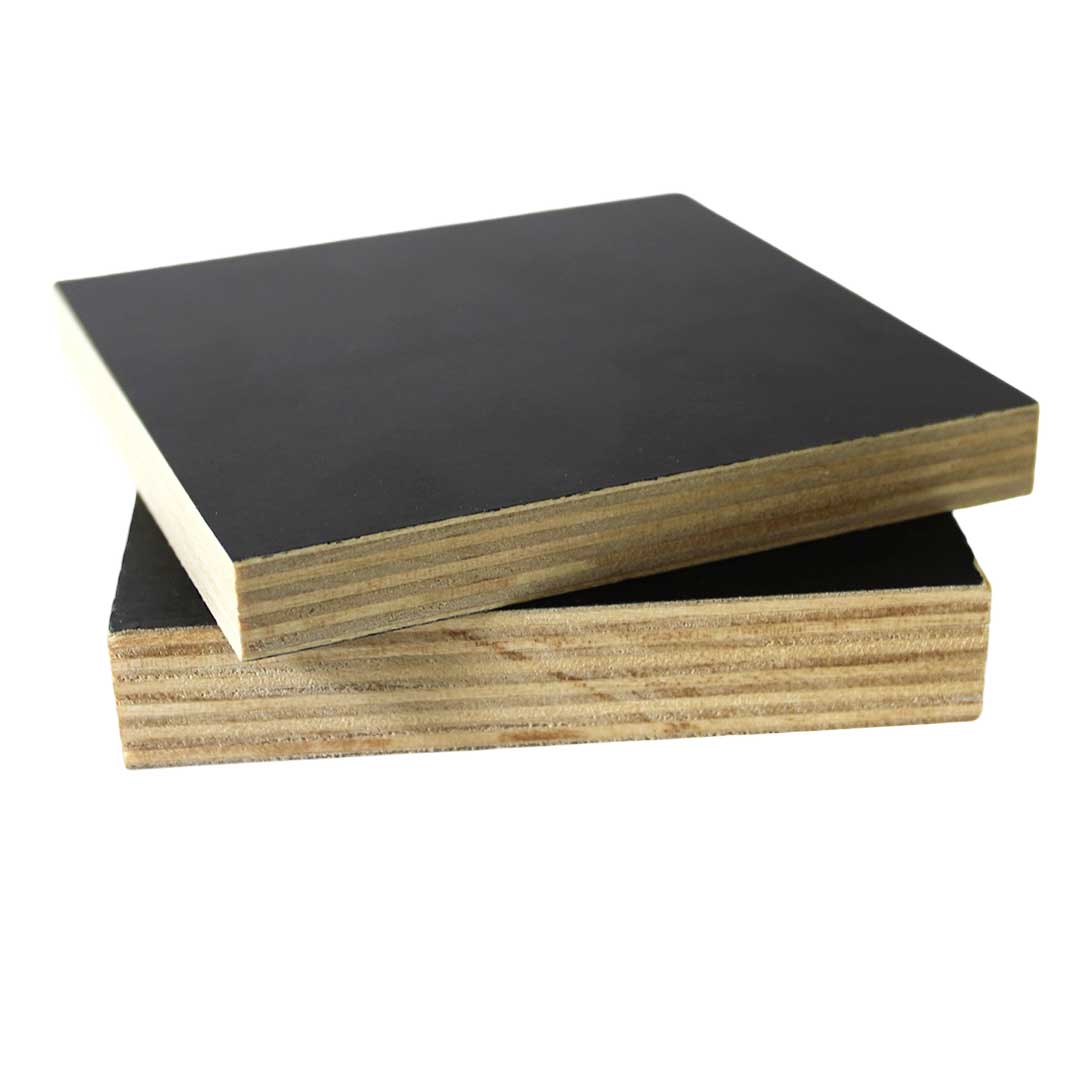
http://Sony’s BMC, Bulk Molding Compound
The cabinet made of Sony’s Bulk Molding Compound (BMC).
Long a fixture in Sony anti-resonant design, BMC is carefully formulated for high strength and high internal loss.
Like steel, it has the rigidity required for its structural purpose. But unlike steel, BMC steadfastly resists vibration and resonance.
BMC consists of calcium carbonate (a principal component of marble), glass fiber reinforcement and unsaturated polyester.
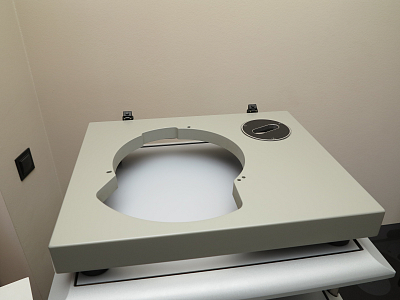
I’m joking about the baltic birch, and it might be a poor choice,
but Linn's is just a lot of thinner layers of beechwood veneer, and nothing but pressure and glue, not separate layers transmitting differently and synergistically,
Or, I’m wrong, it could be a few pregnant termites pressed together at strategic vibration absorbent locations, a proprietary design from years of research for sure.
|
Satisfying Curiosity
I assumed (you know I got kicked in the assss for that) that Sony long ago had developed it's own BMC, but this just popped up, perhaps they just used some stuff available to all
4 brand names of BMC available to all
|
newton_john
ANYONE who would even take the Bedrok seriously, much less buy it,
is ’not yet born’, because their brain is not yet functioning. Less smart than the aforementioned pregnant termite which can at least resonate at the right time in the right place if properly trained.
|
daveyf
you might have surmised, with the recent rise in the cost of termite food, I'm hard pressed, nearly as much as the Bedrok.
|
newton_john
right here on our site, more for Bedrok fans who must have Rocks in their Heads
Rocks
I'll stop fooling with you now,
|
not my proudest moment, but you two should accept some blame for taking me or Bedrok seriously.
|
I had assumed, (like the Denon, JVC and Sony Plinths) that it was solid with only cutouts as needed for more substance. Seems it’s mostly Hollow within.

Does it come with adjustable isolating feet? From 'footfall' comments, it seems all these years they should have been researching proper options
|
The most precise manufacturing tolerance I ever encountered was the extremely tight shaft and bearing of my Thorens TD124.
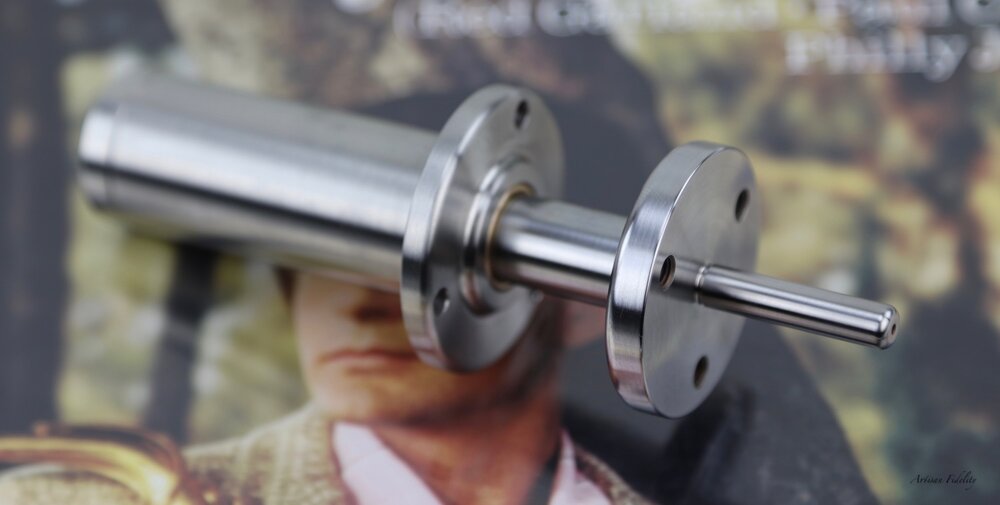
You attach the shaft on the bottom of the 4.5kg (9.9lbs) cast iron platter, place it in the bearing, it takes several minutes for over 10lbs to fully lower, the air has to escape, push it, it is like an air spring, it bounces back. I will never forget the 1st time I put it back in and experienced that heavy platter floating on trapped air.
The many parts of it’s SME 3009 II Tonearm are such that required movement is easy yet impressively tight
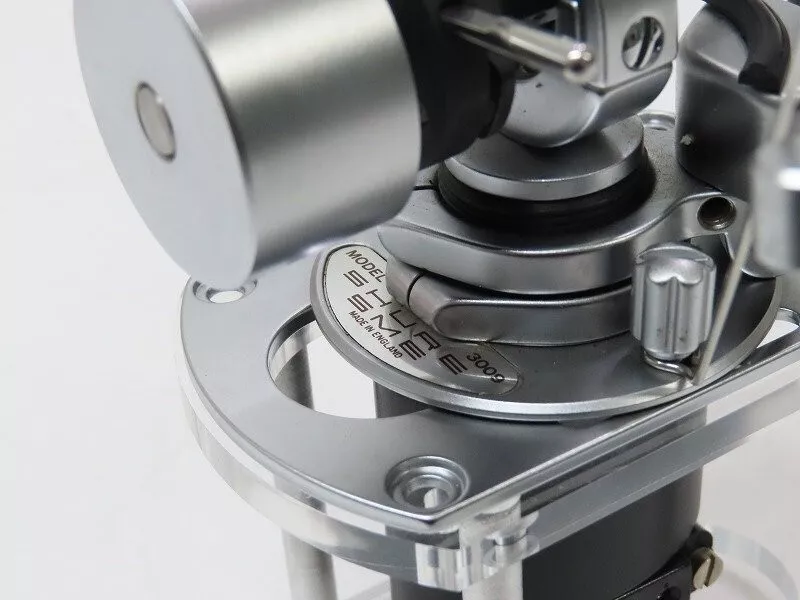
I watched this video showing the assembly of Linn’s TT in a Bedrock Plinth, and I was quite surprised at the looseness of parts, at minute 5, the platter/shaft drops into the bearing, finishing with a clink or clunk, it happens twice and then, the tonearm post goes into the mount like a truck driving thru the Holland Tunnel at minute 6.
The Bedrock’s best feature seems to be captive threaded inserts to fasten the top and bottom metal plates, you can see it’s just an edge frame with corner blocks, not really a plinth in my thinking.
https://www.youtube.com/watch?v=SqP4eHBSlI4&t=2s
I was/am shocked to see the lack of precision, I always assumed fine manufacturing tolerances were part of Linn’s success.
That TD124/SME 3009 II combo combined with the V15VxMR microridge on beryllium produced the most impressive, tightest bass I ever experienced (tracking at only 1.0g). I’ve never forgotten or experienced it since having to part with it because it’s bearing was too succeptible to vertical movement from my springy wood floors.
I always felt quite certain it was due to ALL groove modulation being transferred to the cartridge, none escaping thru movement in the arm and TT. I have to believe that cannot be possible with the loose platter shaft and tonearm post seen in that video.
|
watch the video
https://www.youtube.com/watch?v=SqP4eHBSlI4&t=2s
minute 5, the shaft simply drops into the bearing with no resistance
clunk
he removes it, adds a few drops of oil, it simply drops in again
clunk again.
There is no way in the world that that can be considered fine tolerances. and what makes the clunk noise? shouldn't it be zero contact floating on oil?
minute 6, drop the tonearm post in the mount indicates no close fit either.
|
|
Until you personally experience waiting SEVERAL MINUTES for a very heavy platter to drop into it’s bearing well, you cannot imagine how impressive it is. You mentioned 10 minutes, I am remembering around 6 minutes, just walk away, come back after a while.
I just jumped about learning a bit about the DM101 (I never saw or heard one), it seems it’s bearing, similar fine tolerances to the Thorens TD124 is the key to it’s following, I saw many comments about the springs, center spring, tweaking springs ..... but in all cases it’s the bearing that allows it’s superior bass performance.
I always assumed Linn had similar tight manufacturing tolerances, I remain shocked by what I saw in that video, and still wonder what made the clunk each time it was dropped into the bearing well?
It seems, from comments, the DM101 bottom thrust bearing was less susceptible to vertical movement than the TD124, or those vertical vibrations were curtailed by the softer spring suspension, as opposed to the firmer density rubber mushrooms Thorens used (I had installed new OEM mushrooms),
I built a skirt surround base like the Bedrock, with a continuous ledge (rather than Bedrock’s 4 corner blocks) with a continuous layer of foam supporting a top board cutout for the TD124, reduced but still didn’t solve the problem.
An old discussion here, just over 20 years ago
https://forum.audiogon.com/discussions/anyone-using-a-logic-turntable
simple search results 'dm101'
|
dover
I’ve never seen any Vertere model, that kind of precision is beyond impressive, it’s downright scary.
The fit of the posts of the SME, Acos Lustre, JVC-Victor tonearms are all similar: snug, mated, properly aligned while making refined adjustments.
My 12.5" long tonearm from Russia, the post is not tightly fit, goes into it’s base plate very easily, like the Linn arm does in that video. They think it’s ok if it’s held in place by a set screw. I had them modify the base for 2 set screws (enhanced inconvenience, eh), and I added a layer of very thin tape around the post, a much finer fit, stays aligned while adjusting it’s height (with it’s built-in micrometer which is a nice feature).
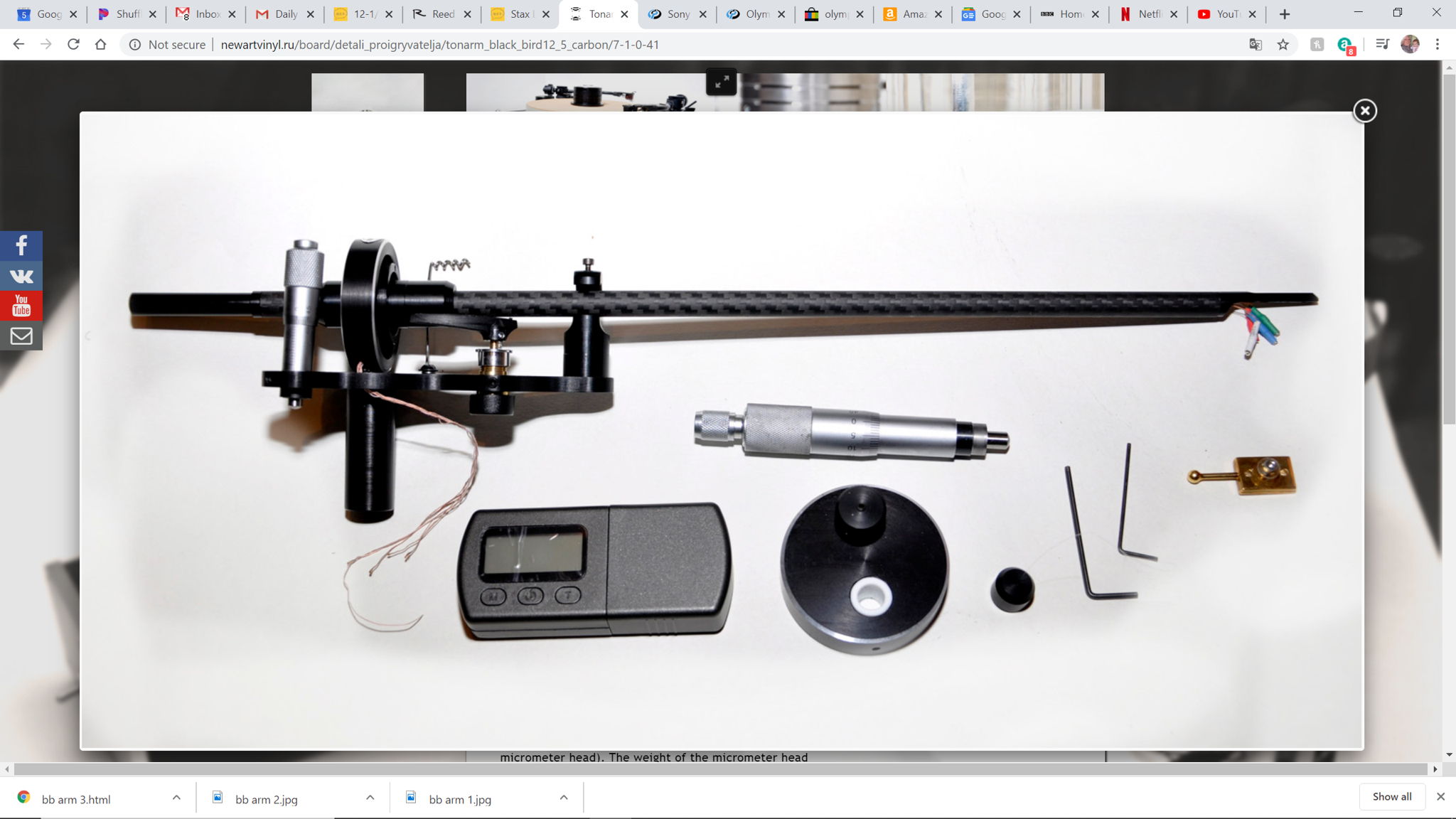
|
mylogic
I found the Datum II and IIs silver wire version, it appears they changed the mount from a threaded post and nut below deck to a Jelco Type surface mounted 3 screw base plate, am I correct about that? I prefer removable headshells. They do not mention it, but I think I read that the Datum II and IIS includes azimuth adjustment at the end of the arm, I see what look like 2 screws
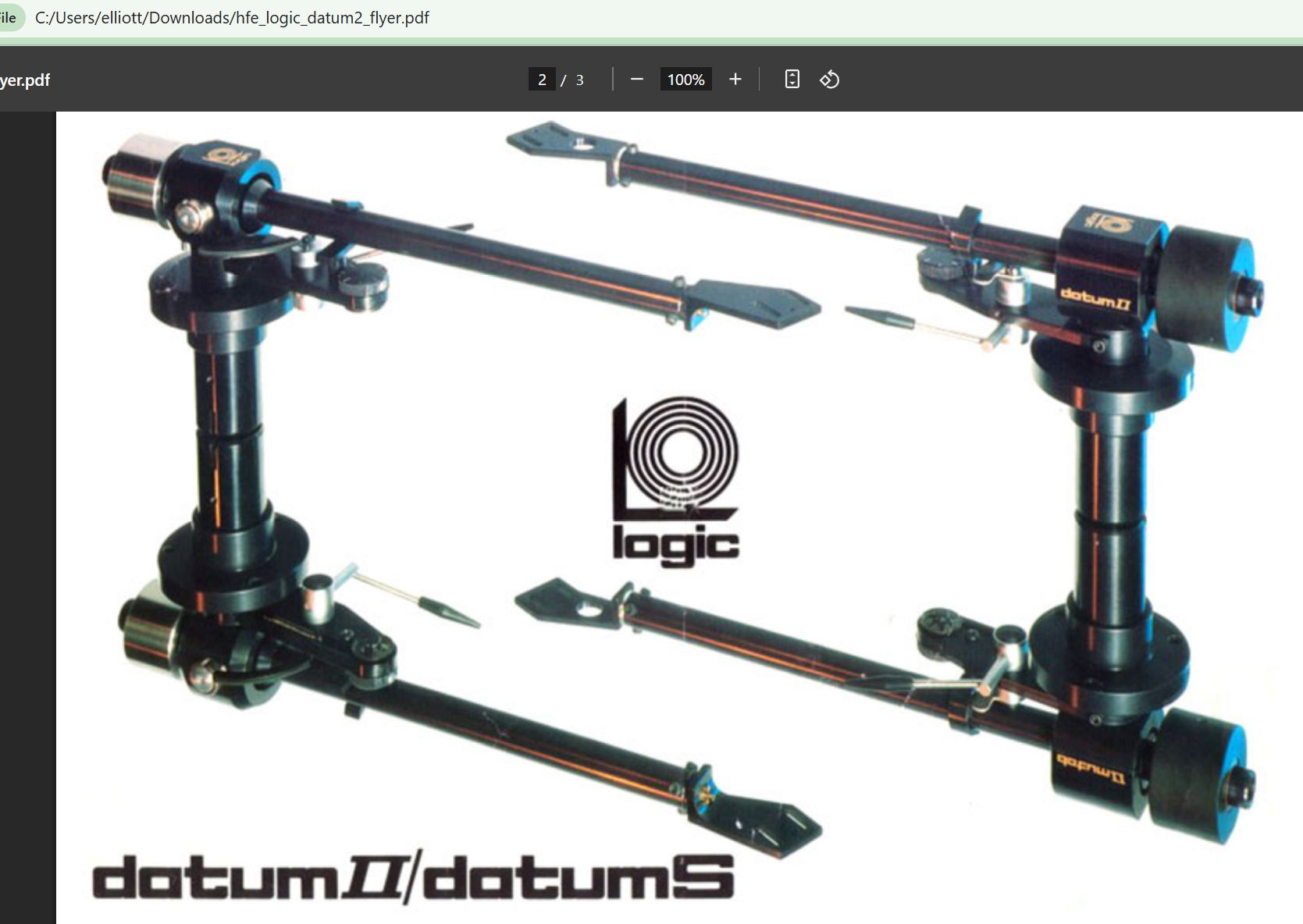
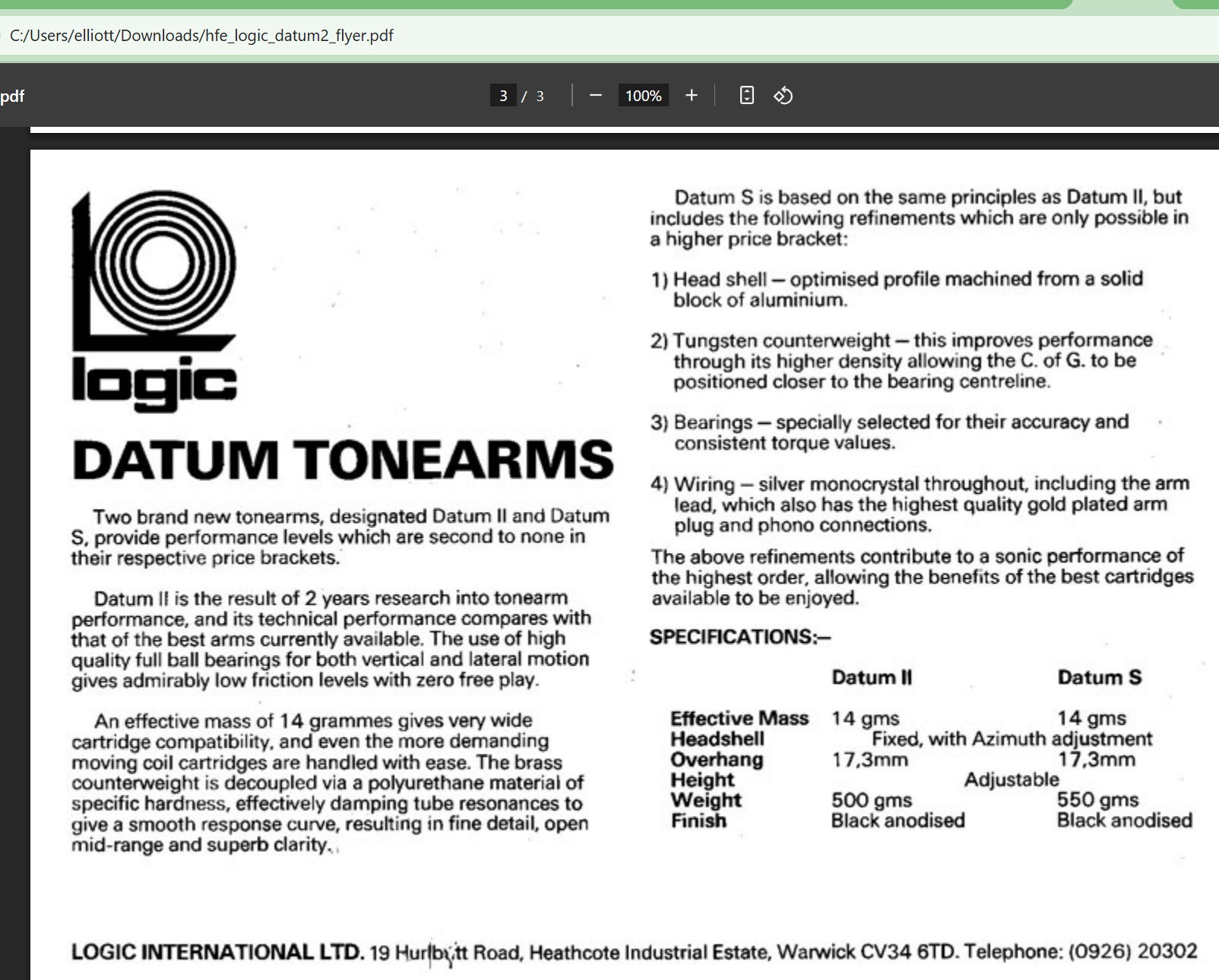
I just mounted my new to me Vintage JVC Victor UA-7082 11-1/8" long arm. It's counterweight section's rubber isolation sag was properly repaired. The anti-skate adjustment is the smoothest I ever encountered, like the Acos Lustre GST-801 it is easy to adjust while playing/listening, although I prefer setting it while lowered onto the smooth side of my alignment disc

. After releasing the JVC height locking ring, then you can place the stylus and adjust the height while playing, however final locking is a two handed job, not while playing.
My Acos Lustre GST-801 which I learned about here is my favorite arm, easy to release/adjust/lock everything while playing: height/tracking force/anti-skate. I use an AT headshell with azimuth adjustment. I wish they made a long version of it.
I just noticed, the Logic Datum II looks to have a very compact/short length counter-weight section, it might fit on the left side where my Mission/Jelco 774 is, I will need the measurement from pivot to the rear end, and I need to double check the overall height for clearance when the dust cover is on
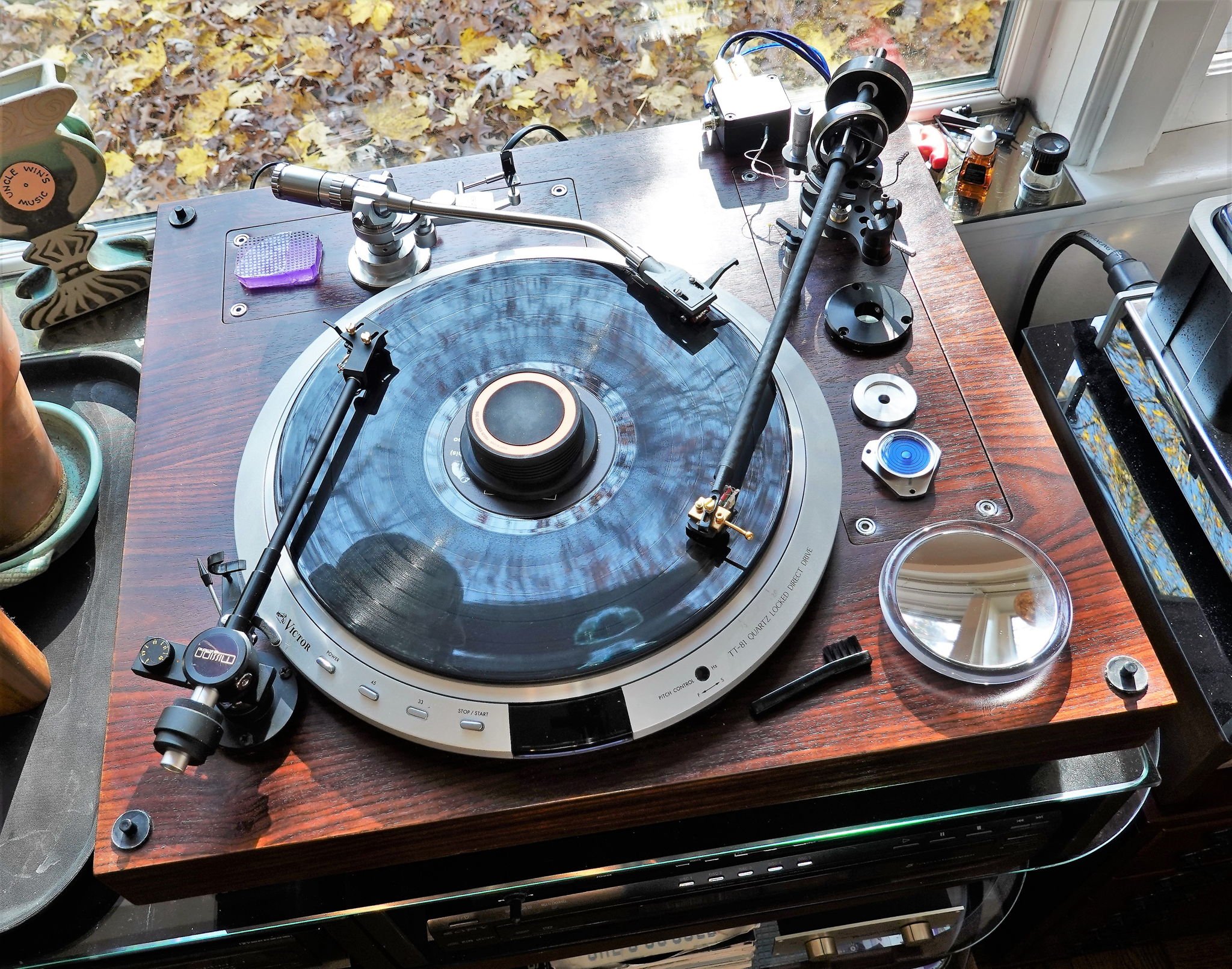
This still shows the 12.5" blackbird arm, I removed it, spun the armboard around 180 degrees, and used the original hole that the 45 adapter is show in, where the original 7082 arm was.
|
|